2019年10月11日に開催した専門性を生かすキャリアパスセミナー「市場を創り出す~未踏の領域でのソフトウェア開発~」の講師にお招きした石井恵三(株式会社くいんと 代表取締役)さんに、数学を専攻している学生と教員に向けて専門性を活かした企業の現場についてお話をしていただきました。
日時: 2019年10月11日(金)16:30~18:30
場所: 理学部3号館2階 第3講義室(3-205)
講師: 石井 惠三 氏(株式会社くいんと 代表取締役)
主催: 北海道大学大学院理学研究院数学部門
共催: 北海道大学物質科学フロンティアを開拓するAmbitiousリーダー育成プログラム/北海道大学大学院理学研究院/北海道大学大学院理学院
海外勢に席巻される前に参入してほしい
みなさんこんにちは。株式会社くいんとの石井と申します。
私は、設計用のソフトウェアの中でも特に構造を最適化するためのソフトウェアを作って、自動車をはじめ製造業で使っていただいています。特殊な例では、あるスポーツ用品メーカーの研究所の方が著名なメジャーリーガーが使用するスパイクを、我々のソフトウェアを利用して10年の間に半分の重さにしたとかですね、そういったところで寄与しています。ただメインは自動車であるとか、電機、製鉄など、結構しっかりしたものを設計する時に軽量化したり、振動の問題を解決するために使われています。
ほぼ35年前に、自分で作ったソフトウェアで日本の製造業になんとか貢献したいと思い会社を立ち上げました。日本のCAE (Computer Aided Engineeringの略 製品の設計・解析用ソフトウエア)は今、風前の灯火でして、海外勢に席巻されるのが時間の問題というところまで来ています。その原因となるのは、日本では数学、物理を修めた方の参入が非常に少ないということです。
海外でこの分野のソフトウェアの研究・開発に活躍されている方々には、数学・物理でPh.D.をとった方が多くいます。その差が今日出ておりますので、今日の私の話を聞いて少し興味があると思ったら、将来ぜひこの分野に参入して下さい。日本をもっともっと元気にして欲しい。
基幹となる技術を持つ
私達の主力の製品はトポロジー最適化、形状最適化、それらから算出された形状をCADに自動で戻すことにもチャレンジをしています。色々やっていますけど、私の会社はいまだに社員は18人しかおりません。我が国のものづくりに必須なCAEソフトウェアの現状が海外勢に押され風前の灯火になっている中、世界で戦っている自動車を代表とする大手の製造業で、どうやって我々のソフトが成果を出して来たかについてお話ししましょう。
私は今の会社を1985年に設立しました。その当時からCAEのソフトウェアというのはだいたい海外の大きな会社の製品がシェアを持っていて、例えばフランスの戦闘機を作っているダッソー。このダッソーが大きなソフトウェア会社を持っていて、航空機・自動車の設計ではCATIAというソフトが世界の航空機、自動車産業を席巻しています。ダッソーの子会社であるダッソーシステムズとか、ドイツのシーメンスに買収されたシーメンスPLMソフトウェアとか、巨大なコングロマリットがCAEの分野のソフトをほとんど席巻してしまっています。日本製は皆無です。そんな状況の中で、汎用ではないニッチなところで、巨大なソフトウェア会社が手を出していないところで、役に立つ分野を見つけて、自分で作って商売をしてみたいと思って会社を作りました。
その時掲げたビジネスモデルは、大学のユニークな研究をもとにニッチでもオンリーワンのCAEソフトウェアを開発しようと決めました。そして、日本の製造業が製品開発をする時に、この自分達で独自に開発したソフトウェアで貢献したいという想いで会社を作ったわけです。
大切だったことは人との繋がり
ジャック・レモン Dr. Jason R. Lemon
話していてハートを抉られるというか、特に感銘を受けた方々が三人います。一人はジャック・レモンさんという方で、1967年にSDRCという会社を創業されて、振動のコンサルティング会社を作り、すごく大きくなりました。でも、彼はビジネスよりも技術に興味を強く持っていました。直接ビジネスに興味がなかったから会社がどんどんどんどん大きくなって行ったんです。
今日我々が使っている「CAE」という世界共通の言葉を作ったのも実は彼なのですね。もともとこの方はシンシナティ大学で助教授をしていて、32歳の時にSDRCという会社を作りました。CAEという言葉を世界に出す2年ほど前に僕は彼から色々な話を聞いて、とにかくCAEという分野にはこんなにたくさん夢があるのだと感じ、自分もいつかはやってみたいと思ったわけです。
ジョン・ホルキスト Dr. John O. Hallquist
二人目は僕と同じ歳で、ジョン・ホルキストという方です。今世界中の自動車会社が衝突のシミュレーションでかなりいい線行くようになったのは、正に彼の功績です。この方はLawrence Livermore National Laboratoryというアメリカの国立研究所で衝突をずっと研究しDTNA3Dという衝突シミュレーションのコードを作っていました。ある時、彼に独立を勧めたら数年後にLSTCという名前の会社を作って、そこから出したLS-DYNAという衝突のシミュレーションソフトウェアは今や全世界を席巻して、ダントツのシェアを持っています。
1982年に僕が初めて彼をLivermore研究所に訪ねた時に、一通り話をした後にお腹がすいたから家に来いと言って、夕飯をご馳走になりながら同年齢ということもあり、FEM、ソフトウェア開発等色々な話で盛り上がりました。帰る時に当時は記憶媒体2400フィートの大きな円盤の磁気テープを5本右脇に抱え、30センチ位のマニュアルを数冊左脇に抱えて、これを全部持って帰れっていうんです。何が入っているの?と尋ねたら、自分がこれ迄に開発したプログラムのソースコードが全部入ってると。国のお金で作ったから平等に与えるので持って帰っていいよってことで、勉強させてもらいました。
菊池 昇 先生 Prof. KIKUCHI Noboru
この方は日本人で35歳でミシガン大学の教授になった方ですが、今は日本に滞在していてトヨタグループのトヨタ中央研究所の代表取締役所長をやっています。すごく偉い方なのですけどとっても気さくな方で、僕は彼と38年付き合いがありまして、「俺と石井さんはコインの裏と表だから死ぬときはお互いにキーボードに突っ伏して死のうな」と固い約束をして(笑)います。
三人に共通することは、徹底的に夢と技術を持っていることです。夢と技術が世の中、製造業に貢献するのであって、技術を遡れば基礎的な学問です。そして、ほとんどが大学で教えていた経験があって、その経験を活かそうということで企業に行ったのです。だから三人共、基礎学問が非常にしっかりしていること。これが一番大事です。
基礎学問をやらないで応用を先にやる人は99.9%失敗する。そう言うことを語り合いながら、彼らとは比較にならないプアな私も、勢いで会社を作ってしまったわけです。
3つのこだわり
私は35年会社をやっていて、これら3つのこだわりがあったから、今ここにいるのだと思っています。
1番目は、やはり先ほどの先人達から得た夢ですね。CAEの分野でたとえ規模が小さくても、海外の何千人の巨大な会社じゃなくても、利用する人々にアイディアを提供できるような革新的な純日本製のソフトウェアを開発する。
2番目は、自分の目的はお金儲けじゃないってことです。先ほどの三人の方もそうですが、ソフトウェアを利用される製造業がより良い製品を開発するためのお手伝いをしようと思いました。
3番目は、挑戦・チャレンジですね。頑なに他人のモノマネはしないと決めました。こんな事を言うとどんどん自分が窮地に追い込まれる。でも他人のモノマネはしない。オリジナリティにこだわって、常に新しいことにチャレンジを続けようと。これは非常に大事なことです。他人の二番煎じを行ったところで、それは巨大な資本が乗り込んできた時には、あっという間にやられてしまいます。
構造最適化は余分な皮下脂肪を取ること
数学に限らず学問を修めることははすごく大変だと思うのですが、自分がバカになれた時に一段上がれます。それから自分がハングリーになった時に追求ができます。これだけは自分の経験としてお伝えしておきたい。(Steve JobsがStanford Universityの卒業式で講演した時に言った有名な言葉です。)
私は離散化手法としての有限要素法をほぼ50年、構造最適化を35年くらい基幹となる技術としてやって来ました。構造最適化って何をやるかというと、やることは簡単で、ビールばっかり飲んで膨らんだお腹の皮下脂肪を取ることです。
構造物に当てはめると、押さえるところと荷重を掛けるところがあって、力に抵抗する構造物で、もう少し材料を減らしたいときに、表面を削っていくやり方が形状最適化です。これ迄色々な手法が提案されていて、形状最適化は80年代で終わったと言う人々もいたんです。ところがどっこい、さらに新しい理屈をちゃんと研究し続けた方がおられて、お腹の皮下脂肪をもっと綺麗に取り除く技術が今はできています。これが形状最適化です。
ところが、お腹の脂肪だけではまだ足りないというストイックな人がおられた場合に、どうすればいいかというと、お腹の皮下脂肪の他に内臓脂肪も取りましょうと。一生懸命内臓脂肪も取ると、内臓っていうのは体の中にありますからそこに穴が空くわけです。これは究極の最適化でして、ものすごく質量が減ります。
ただこれには1つだけ欠点がありまして、このように構造物の中に穴が空いているものをどうやって作るんだという、製造の過程で問題が出ます。それを近年解決したのが3Dプリンタというハードウェアです。
ところで、連続体のトポロジー最適化という技術がどの時期にどこから出てきたかというと1988年に論文が初めてパブリッシュされたのですが、デンマーク工科大学の数学科の教授で、マーティン・ベンソーという方と、ミシガン大学の菊池昇教授がサバティカルでデンマーク工科大学に滞在してた時に、二人で話し合って作ったのがこの連続体のトポロジー最適化という概念なのです。
この論文は30年経った今でも、世界中からアクセスされていて、日本人の中のアクセスのランキングではベスト3に入るくらいの論文です。この論文がすごくユニークだったのは、前述の内臓脂肪とか皮下脂肪を取ろうとするときに、対象となる構造物が材料で埋まっていても、中に小さな穴がいっぱい空いている多孔質体と仮定したのです。なぜ多孔質体と仮定したかというと、彼らはその時に応用数学分野でフランスのLionsらにより研究されたhomogenization methodというものを既に知っていました。フランスの故ジャック・ルイ・リヨンス先生からhomogenization methodの講義を直接聞いて、これを工学的に応用できないかを考えていて、できたのがこのトポロジー最適化です。
多孔質体を仮定すると便利なことがあって、これに最適化をかけると設計変数はこの多孔質体の穴の大きさになります。周期的に空いていますから、ある領域の周期構造の最小単位をユニットセルとして、そのセルの中の穴の大きさを調整することで穴が極限まで大きくなるとそこは材料が存在せず、穴が充分小さくなるとフルマテリアルの状態になります。その間はコンティニュアスに補間する。これで最終的にやってみたら例えばこの上の形が下のような形になって出て来るわけですね。
このトポロジーオプティマイゼーションが30年経った今では世界中で花盛りで、WCSMO(World Congress on Structural and Multidisciplinary Optimization)という構造最適化の世界会議がありますが、これは30年以上の歴史があって、2年に1回やっていて、最初の第1回の会議でトポロジーオプティマイゼーションっていうタイトルで発表した人は数名だったのが、30年経って全体で1200編の発表の内2/3はトポロジーオプティマイゼーションになっているんです。そのくらい30年経って、どんどんどんどん広がっています。
私はその時に最初の論文をベースにソフトウェアを作りました。論文が発表になったのが1988年、翌年には商用のソフトウェアOPTISHAPEを出しました。自動車会社を始め色々な会社を回って利用をお願いしました。十数年経ってシュプリンガーという本屋さんからTopology Optimizationという分厚い専門書が出ました。Software for Topology Optimizationという章がありまして、なんと1989年に「くいんと」という日本の会社がOPTISHAPEという名前でコマーシャルソフトウェアをリリースしたと書かれていました。我々が第一号だという証明で大変嬉しかったです。
(2)につづく
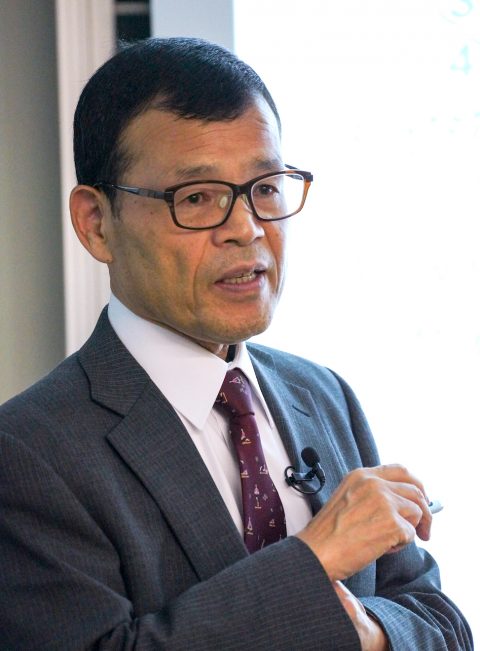
石井 恵三 ISHII Keizo(株式会社くいんと 代表取締役)
1948 年、神奈川県横須賀市出身。1970 年、日本情報サービス株式会社(現、株式会社JSOL)に一期生として入社。1985 年 株式会社くいんと設立、代表取締役社長として現在に至る。 「位相最適化の応用に関する研究」で、2002 年、東京都立大学において博士(工学)の学位を取得。日本計算工学会より功績賞(2012)、技術賞(2015)を受賞。日本計算工学会フェロー(2013)。趣味はドライブと映画鑑賞。